高成本效益的實用系統方法解決QFN-mr BiCMOS器件單元測試電源電流失效問題
2.6 FMEA:
本文引用地址:http://www.104case.com/article/201703/344836.htm項目組還運用FMEA故障模式和影響分析法重新考慮變量關系。因為電源電流沒有故障模式,所以考慮從因果矩陣導出的全部KPIV變量,如圖11所示。(詳圖見附錄C)

圖11:故障模式和因果矩陣
2.7 兩個速效方案:
在完成上面的分析后,立即發現兩個(2)速效方案。

圖12:臨時措施矩陣
實驗結果分析
A. 流程圖
· 這個項目覆蓋18個流程工序。
· 15個工序或83%是VA(增值),3個工序或17%是(無增值)
· 未發現隱藏工廠
· 在輸入-輸出工單中發現42個潛在X’因素。
B. 因果矩陣
· 運用因果優先性分析法找到5個潛在的X因素。
C. FMEA
· 因為電源電流最初沒有被識別為故障模式,所以5個潛在X因素都被視為高風險。
D. 速效方案
· 發現2個速效方案
3.1 驗證方案

圖13:驗證方案矩陣
? 運用比例測驗法驗證GAP分析法產生的兩個(2)項目(烘烤測試)
? 運用混合水平DOE法驗證三個X。
(詳圖見附錄D)
3.2 統計檢驗
通過觀察圖14的統計假設檢驗結果不難發現,水刀后面的烘烤工序影響電源電流抑制比。
實用性結論:電源電流抑制在無水刀工序時較低,R-square值為22.78%,可信度高于95%。如果不采用水刀工序,電源電流抑制比較低。

圖14:假設檢驗
3.3 驗證方案

圖15:驗證結果
驗證結果(圖15)顯示,電源電流抑制比受水刀后面的燒烤工序影響,因此,如果無水刀工序,則抑制比會降低。
根據已發現的關鍵X因素,例如,輸送帶速度、烘烤溫度和水刀壓強,項目小組運用試驗設計方法進一步改進水刀工序。
(詳圖見附錄E)
3.4 試驗設計(DOE)
運用試驗設計法分析輸送帶速度、烘烤溫度和水刀壓強參數,目標是確定和設置使電源電流失效率最小化的最優參數。
圖16所示是試驗設計方案,用于優化水刀關鍵參數。
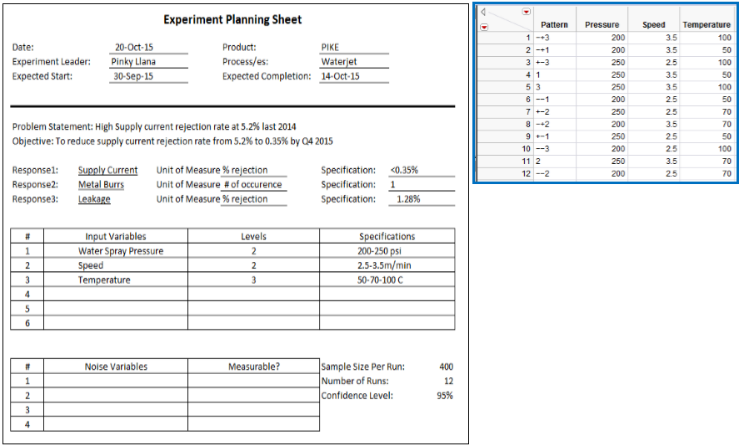

圖16:試驗設計方案和結果
(詳圖見附錄F)
從試驗設計結果看,當P值是0.0231時,壓強是影響電源電流抑制比的主要因素。當R-Square值是0.8997時,壓強與速度交互作用(P值是0.0231)、速度與溫度交互作用(P值是0.0242)、壓強與溫度交互作用(P值0.0405)是影響電源電流抑制比的主要因素。
根據圖17預測剖析圖給出的最優設置,最大理想參數是在壓強 = 200psi, 速度 = 3.5m/min,溫度 = 50 degC時取得的,在這些參數條件下,電源電流抑制比為-0.238+/-1.156,泄漏為0.414+/-1.84,金屬毛刺為1.338+/- 4.63。
在P值 = 0.0231時,壓強是影響電源電流失效的主要因素;在P值 = 0.0231時,壓強與速度交互作用也是主要因素;在P值 = 0.0242時,速度與溫度交互作用是主要因素; 在P值 = 0.0405時,壓強與溫度交互作用是主要因素,可信度高于95%。
試驗統計發現,當P值 > 0.05時,這些主要因素及交互作用不影響泄漏比和金屬毛刺。
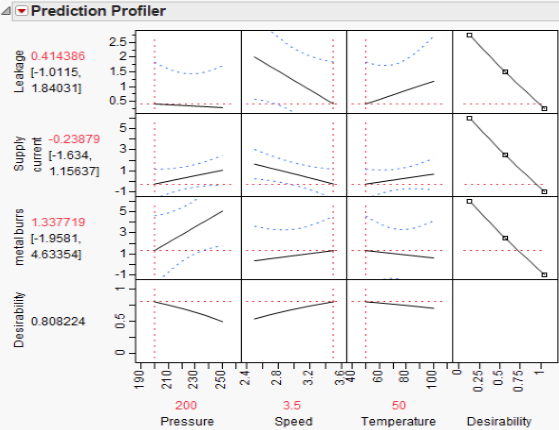
圖17:預測刻畫器剖析表
觀察預測刻畫器報表不難發現,當壓強為200psi,速度為3.5m/min,溫度為50 degC時,電源電流抑制比、泄漏和金屬毛刺三個參數取得最優值。
3.5 試驗設計(DOE)結論
在P值 = 0.0231時,壓強是影響電源電流失效的主要因素;在P值 = 0.0231時,壓強與速度交互作用也是主要因素;在P值 = 0.0242時,速度與溫度交互作用是主要因素; 在P值 = 0.0405時,壓強與溫度交互作用是主要因素,可信度高于95%。
試驗統計發現,當P值 >0.05時,這些主要因素及交互作用不影響泄漏和金屬毛刺。
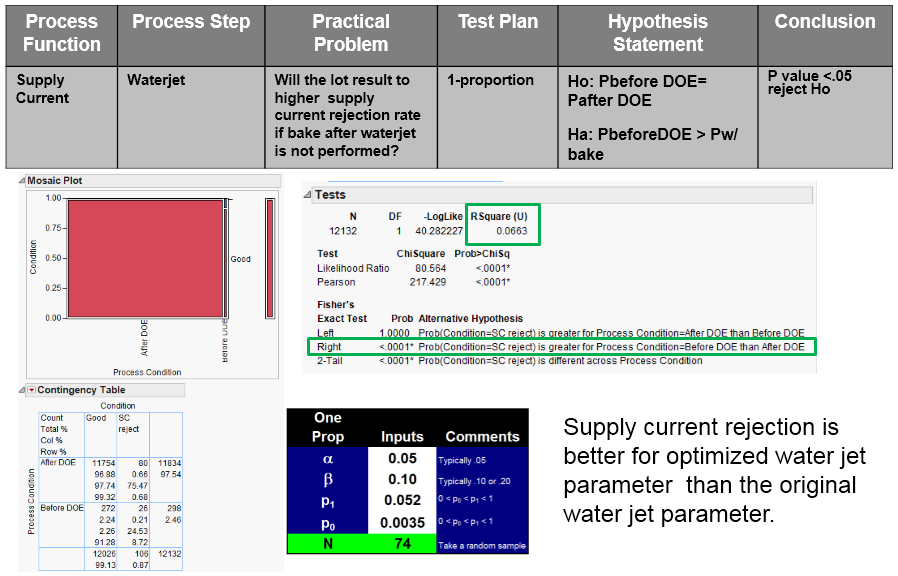
圖18:結果驗證矩陣
(詳圖見附錄G)
3.6 水刀是如何影響產品1電源電流失效的?
了解失效機制知識有助于提高統計結果的準確性:
? 封裝滲透率或高速水分子引起的摩擦磨損效應隨水刀壓強升高而提高。
? 高溫鼓風機(相同壓強)使氣體分子動能更強,增強摩擦磨損效應。
? 膠帶速度效應最有可能影響摩擦磨損(接觸速度),不過只限于鼓風機區,無水環境會逐漸消耗摩擦磨損效應。
3.7 實現結果
意法半導體卡蘭達工廠取得0.35%的電源電流抑制比(外包廠基準),較試驗前的5.2%有巨大改進。
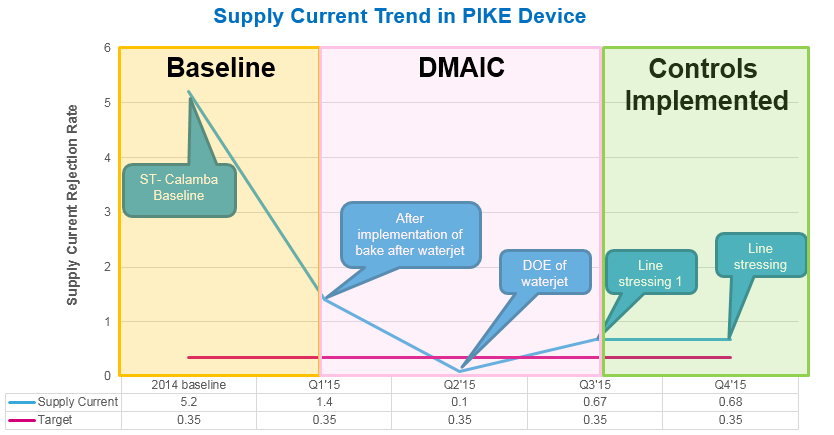
圖19:電源電流抑制比趨勢分析
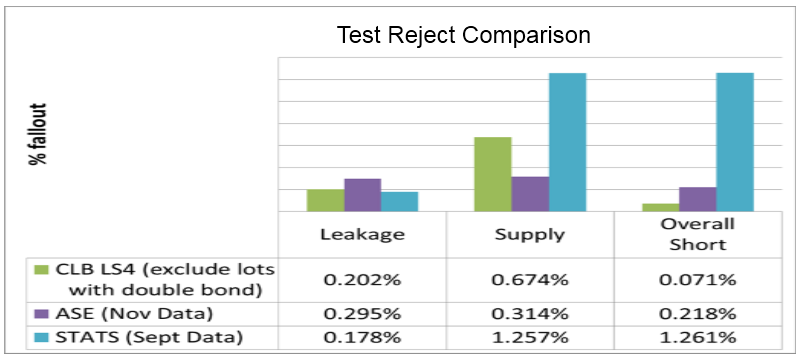
圖20:意法半導體卡蘭巴工廠與外包廠比較表
評論