可編程序控制器在銅冶煉生產過程中應用
PLC主要對一些給液泵、循環泵、泥漿泵等一些泵的啟、停進行聯鎖控制和監視,對風機的運行情況進行監控,對短路器進行監控。
由于采用了PLC,取消了大量的二次儀表,所有的儀表指示值都可以在監控站的屏幕上顯示,統計報表、歷史趨勢曲線都可以很方便地打印出來。參數的修改和設備的操作都可以用鼠標在屏幕上完成。
三、網絡化方案及其實現
PLC-5處理器不僅具有非常強的控制功能,還具有非常強的通信能力。因此,它不但適用于各種控制應用環境中,特別適用于計算機集成生產系統(CIMS)的生產方式,與計算機等來形成一個高度全面化的分布式多級控制系統。生產的過程十分復雜,因此實現生產過程的全面高度自動化比較困難,同時,由于市場需求和技術發展的更新速度日益加快,以往傳統的、相對穩定的生產過程也變得越來越不適應要求,這就對自動化生產的方式提出了一個動態的開放要求。因此,管理和控制一體化成為現代化企業越來越迫切的需要,而在此過程中,網絡化的實現又成為一個關鍵的環節。
金隆公司的生產管理網絡就是這樣一個集控制和管理于一體的廠級分布式控制系統,網絡構成如下圖所示。
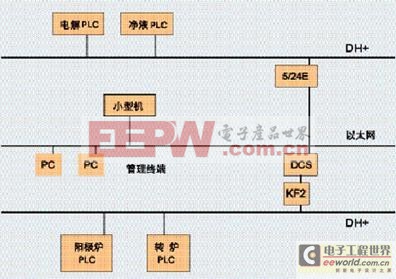
1. PLC與管理網的聯接
由網絡圖可以看出,全廠的PLC共構成兩條數據高速通道(DH+)鏈,一條是電解、凈液的PLC通過ROCKWELL公司的以太網接口模塊 5/20E與以太網相連,一條是陽極精煉爐、轉爐的PLC通過DCS與上位以太網相連。采用這種聯結方案主要是受各PLC物理位置的限制。PLC的實時數據傳到以太網后,由美國DEC公司的阿爾法小型計算機接受并轉換成個人電腦可以識別的數據信號后,再發往各管理終端。這樣,各管理終端通過相應的軟件就可以隨時調出工藝流程畫面和實時工藝參數,管理者就可以隨時了解到現場工藝情況和各類數據報表,從而為管理帶來極大的便利。
2. DH+網
DH+是一個公共總線形成的對等的工業局域網,其網上的每個節點無主次之分,網絡的存取方式為令牌傳遞方式,傳輸介質為屏蔽雙絞線,最大傳輸距離為3044m,通信波特率為57.6K(57.6K位/s=1字節/0.14ms),最大節點數為64個。
屏蔽雙絞線相對比較便宜,并有比較好的抗噪性,能保證傳輸信號不失真,不失為一種理想的傳輸介質。令牌傳遞方式可以消除那些試圖獲得網絡訪問權的 PLC站點之間的競爭,哪個站點得到令牌,它就成為主站,從而有權向其他站點發送信息,用完相應的時間片后,即將令牌傳遞到下一個站點,這樣可以避免因某個站點故障而影響到整個網絡。每個PLC-5/40處理器有四個通信口,可用軟件設置成遠程I/O通信鏈與輸入輸出機架相連或設置成DH+網絡通信口。在轉爐調試時,由于各站點之間需要傳遞的數據量太大,引起監控站屏幕頻繁出現網絡超時報警信息,我們就用處理器空閑的通信口,專門設置了一條DH+通信鏈,專門用于處理器之間的數據傳遞,解決了網絡擁擠的問題。
由于DH+網絡優越的網絡性能,使得數據在站點之間傳遞變得極為便利,行車稱重數據本來發往陽極精煉爐,可是因為有了DH+網絡,在轉爐也可以看到這些數據。轉爐的作業方式是交替作業,加上很多設備是三臺轉爐共用,因而需要相互傳遞的信息量非常大,因為有了DH+網絡,一切問題迎刃而解。
四、調試中遇到的難點及解決辦法
投產前,網絡安裝測試好之后,開始進行系統的總調試,發現由于三臺轉爐的很多輔助設備是共用的,因而各PLC之間需通過網絡交換的數據量特別大,引起網絡繁忙,網絡超時報警頻頻出現,影響調試和正常操作。起初試圖通過增大監控站的內存、擴大緩沖區、精簡操作畫面等方法解決這個問題,但效果均不理想。后來想到利用處理器的其他空閑的通信口,專門開設一條網絡專供轉爐的四個PLC之間傳遞數據用,結果十分令人滿意,很好地解決了這個問題。
五、投產后的增設及改進項目
由于工藝狀況和設備狀況的要求,投產后在轉爐進行了一系列的改造和增設項目,主要包括以下幾個方面。
1. 轉爐事故傾轉的改造
在原設計中,轉爐的事故傾轉是蓄電池帶動直流電機驅動的,由于蓄電池只能供電10min,而充電時間需10多個小時,且有傾轉速度慢、性能欠可靠等缺點,容易引起堵風眼事故。針對這種情況,我們在軟件上進行了修改,使得只有交流失壓時,才由直流電機驅動轉爐移動,在其他條件下,均由交流電機帶動爐子做事故傾轉,大大減少了事故的發生,具有很好的效果。
2. 增設富氧改造調節回路
投產一段時間后,為了增加固破和冷銅的處理量,根據工藝要求,我們在轉爐增加了富氧錘煉自動調節回路?;芈吠队煤?,操作人員只要在操作畫面上設定所需的用氧濃度,調節回爐即可根據送風流量和設定氧濃自動調節氧氣的流量,操作十分方便。至今,使用效果一直很好。
3. 增加純水槽自動補水回路
純水槽的水是用于轉爐冷卻水套的,一旦斷水,就會對設備造成損壞。未改造之前轉爐純水槽補水需用電話與純水站聯系,這就要求操作人員經常監視純水槽的水位,很不方便,改造之后,低水位自動補水,高水位自動停水,且有高、低水位報警,既方便又安全,得到操作人員的好評。
4. 增加報警點和歷史趨勢記錄
轉爐投產后,我們在轉爐增加了PLC系統不間斷電源(UPS)掉電報警、煙罩斷流報警、純水槽水位報警等,提高了生產的安全性。增加了排風機轉速和輸出給定值的歷史趨勢記錄,給設備監護和故障判斷分析提供了依據。
總之,可編程序控制器因其可靠的性能、卓越的控制功能和強大的通信功能在金隆公司的生產和管理中發揮了很大的作用,創造了一定的經濟效益。隨著其性能價格比的提高,相信會在工業企業中得到更加廣泛的應用。
評論