模塊化/KSK 線束自動化設計
深入了解模塊化過程
如圖2所示,模塊化過程必須支持半成品組件。模塊2和3中的電線在終點被分配至模塊1中的連接器。出現這種情況,可能有兩個原因:
1. 模塊1屬于始終存在的“核心”元件,以便來自模塊2和模塊3的導線有終點可去,或者 …
2. 模塊1由模塊2和3控制
需要注意的是,圖2中的線束進行了簡化,實際產品可能更加復雜,擁有許多模塊化元素。由于材料最終將組裝進成品中,這個過程必須保持分布在幾個或多個模塊中組件間的關系。模塊化過程必須考慮進組合模塊的影響,如線束周圍的配管和捆扎等因素。
定義一個模塊化線束系統的過程包括4個不同階段。首先需要電氣系統數據和必要的線束分割信息,接下來需要:
1. 確定模塊代碼和它們之間的關系,包括表示出排他/相容關系等。例如,必須為支持低音炮的模塊(作為消費者的可選功能)設定一個相容的音頻系統模塊。
2. 指定模塊代碼來區分主線束范圍內的導線。這是分配所有其它材料至其所參與模塊的第一步。
3. 分配所有其它材料至各自模塊。“材料”包括連接器和包扎物以及附屬的零件,如端子、密封圈和插頭。在這一步,模塊關系邏輯指導著每個分配的先后順序。例如,如果一個連接器只包含模塊代碼相同的導線,功能模塊分配工具將按照導線代碼進行分配。但是如果連接器包含不同代碼的導線,這個工具則必須考慮核心模塊特性、優先順序以及相容/排他關系,并在適當的情況下建立技術模塊。
4. 定義技術模塊。不可能每次都能將所有東西部署在現有的模塊中。例如,可能存在一個接頭連接著屬于多個功能模塊的導線,那么這個接頭的配置則取決于用在終端產品中模塊的準確組合。解決方法就是一些也被稱作“最后組裝模塊”的技術模塊。它們是多個功能模塊共享材料的集中點。技術模塊還有助實現準確的成本核算,包括額外的組裝材料和時間。
在整個工程設計和制造過程中,無論是線束/衍生線束還是模塊化設計方法都不能使用戶局限于一個選擇。原始設備制造商和供應商可以根據企業的商業模式和終端用戶需求選擇其中任何一種,如圖3所示。
“生產模塊”類別見圖3。它描述了為了制造方便和提高取用率而配置的組件。“生產模塊”可以分開或組合功能模塊的子集,從而簡化組裝和庫存要求。
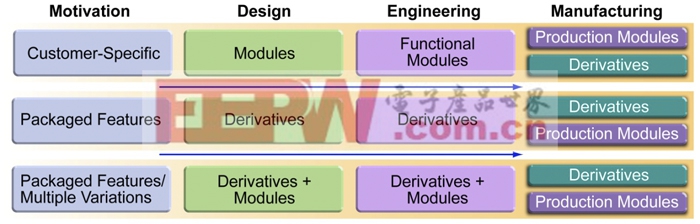
圖3:在整個工程設計和制造過程中,無論是線束/衍生線束還是模塊化設計方法都不能使用戶局限于一個選擇。
設計自動化工具助您一臂之力
如果所有這些讓人難以理解,那是因為到目前為止還沒有強調設計自動化軟件在解決線束設計復雜性問題方面的作用。事實上,當今功能齊全的電子系統設計 (ESD) 解決方案能夠加快和簡化設計階段對模塊代碼的定義,并且加快工程階段對功能模塊的材料分配和制造階段對生產模塊的材料分配。
先進的自動化工具可協助設計師完成模塊化合成和后續步驟。在圖4中,汽車拓撲圖作為模塊化合成前后視圖的背景。在合成之前,電子信號與拓撲掛鉤,但還未整合到布線中。系統被分割成線束,在這個階段,線束中只有用于設備分布的線束段包和位置槽。
此流程開始時就已知道每根導線支持的功能和各功能之間的關系。完成后,電線、多芯線和接頭與各個線束進行配對,所有模塊代碼均被合成。模塊代碼可能與功能選擇代碼一對一,抑或是代表一連串選項表達式。功能模塊被劃分到汽車內各個線束系列中,包括車身模塊、車門模塊、儀表板模塊等。
這些操作可概括為:
* 合成所有導線,不考慮線束層面
* 合成后,自動為導線分配模塊代碼
* 每個線束內擁有相同選項表達式的導線視為相同功能模塊的一部分
* 為沒有選項表達式的導線賦予核心模塊代碼
如果一個設備在邏輯設計中沒有選項代碼,那么合成工具即認定其并非可選設備——平臺中的所有汽車都包含這種設備。它向導線分配核心模塊代碼,確保其應用于平臺中的所有汽車。
相比之下,如果信號用于多個選項設備(按照邏輯計劃),那么模塊化合成工具可以通過一連串相關的選項代碼來計算模塊代碼。現在,可通過針對某項具體可選功能的準確布線來選取功能模塊。
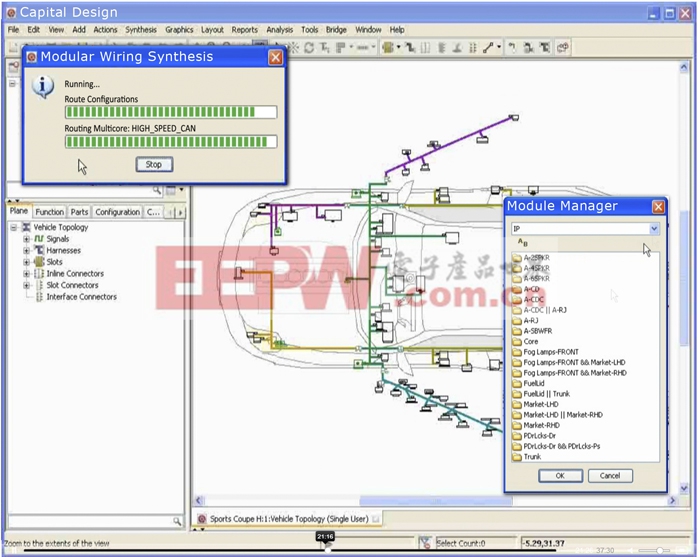
圖4:模塊化布線合成產生模塊代碼,為之后的自動模塊化工程步驟提供支持。
結論
運輸領域原始設備制造商及其線束供應商不斷與復雜性抗爭。原先比較小眾化的模塊化布線系統逐漸獲得認可,這是因為它們可實現高度定制,同時降低控制復雜性的難度和成本。但是,若沒有強大的設計自動化工具的輔助,模塊化方法本身也可能變得很復雜。如今的領先設計平臺是一項可行的技術:它們可以在從電子系統設計(模塊化合成)到線束工程(模塊化細分和分配)的整個過程中自動完成與模塊化設計相關的具體工作,從而提供可靠的配置,同時最大限度地減少贈品和其它折中措施。本文引用地址:http://www.104case.com/article/185527.htm
評論