抽油機井變頻柜在油田現場的應用詳細介紹
本文引用地址:http://www.104case.com/article/160792.htm
這4口井是2005年新投的油井,經過初期短暫的高產后,日產液大幅度下降,平均泵效僅為10.7%,平均系統效率僅為6.1%。除118-160井外,其它三口井沖次己經接近最小,無法調小沖次。
2、試驗井效果
(1)、沖次任意調節
不用更換皮帶輪,不需停產調節速度,提高了生產效率。解決了因調速造成的停產和沖次無法調小問題。
(2)、分段轉速控制
通過變頻對抽油機轉速的調節,根據抽油機的特殊工況,把轉速控制細劃為上沖程轉速控制和下沖程轉速控制,減少漏失,提高泵充滿程度,提高泵效。
(3)、提高油井的產量和泵效
根據油井的實際供液能力,動態調整抽取速度,使油井的供排協調,減少泵的空行程,提高泵效。4口井,提高泵效16.58%,日產液提高0.5,日產油提高0.2。
(4)、提高功率因數
使用變頻器后,電動機功率因數提高到接近1,從而減輕了電網和變壓器的負擔,降低了線損,節省了無功損耗的電費。
(5)、對電網和設備無沖擊
當電機在工頻狀態下啟動時,啟動電流相當于5~7倍額定電流,對抽油設備和供電電網造成很大的沖擊,尤其是118-160井稀土永磁電機在啟動瞬間產生很大的電流和震動,使用變頻后電機柔性啟動,使啟動電流降至3-4倍,減少了對電網和抽油設備的沖擊。
(6)、改善了抽油桿受力狀況
光桿抽油速度對抽油桿受力有很大的影響,變頻降沖次和優化上下沖程速度實現上慢下快,改善抽油桿循環特性。
(7)、提高系統效率
變頻器應用油井使供排協調,泵充滿程度提高,改善桿管應力,提高了井下效率;減少地面無功損耗,提高了地面效率,整體上系統效率明顯提高。
(8)、減少電機能耗
油井調小頻率,平均輸入功率減少3.66kw,平均噸液耗電減少27.62kw.h,平均日耗電減少87.78kw。
(9)、負功能夠回饋電網
對生產中的負功,使用回饋式制動單元,能把再生電能回饋電網。內部已經安裝有電抗器和噪聲濾波器,全程噪聲過濾,不會污染電網和干擾其他設備。
(10)、減少熱洗清蠟的負影響
油井熱洗時,調頻提高沖次,增加理論排量,強排生產,可以明顯縮短含水恢復期,減少影響產油量。
六、經濟效益分析
⑴產出費用
①節省電量費用:
3.66kw×24h×360d×0.47元/kw.h=14862.5元
②少影響產油量費用:
洗井影響:1445元/噸×2噸/次×10次=28900元
③增產量:
1445元/噸×0.2噸×360天=104040元
合計:14.7802萬元
⑵投入費用
①設備投入費用:整套設備投資32000元
這套裝置投入產出比是1:4.618,而且這套裝置壽命較長,可以長久使用,經濟效益非??捎^。
七、結論
從變頻器應用現場數據分析,變頻器一次性投入較高,但解決了機械采油系統功率因數低、電機啟動轉矩大、負載率低、能耗大的問題。電機起動性能良好、功率因數提高到0. 98 、節電率達40 %以上。
◎變頻后無極調速,調速范圍廣,調速過程平滑;
◎調頻后功率因數接近1;
◎柔性起動,可大幅度降低對供電變壓器裝機容量的要求,并使電機振動及噪音大大減小。
◎降低抽油泵容積損失,提高了泵充滿系數。
◎抽油機運轉性能得到改善,動載荷明顯減少,載荷線光滑平直。
◎減少桿管磨損次數,改善桿管受力狀態,延長桿管壽命;
◎降低電機輸入功率和油井噸液耗電。
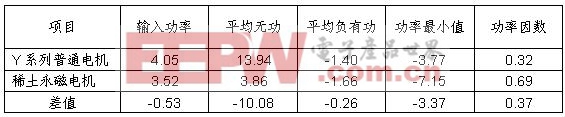
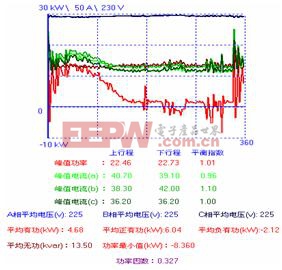
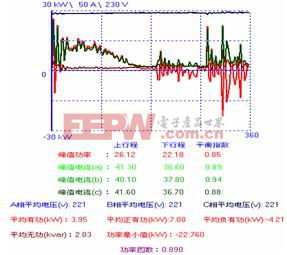
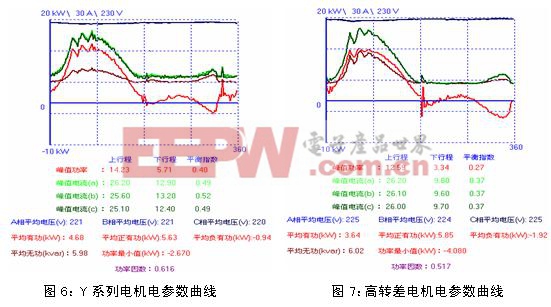
③Y一△轉換
Y一△轉換適合功率利用率低、大馬拉小車嚴重的抽油井使用。電機三角形啟動后,再將定子繞組切換成星型接法運轉。轉換后平衡變差,如果角接時平衡性差,轉換后平衡性更差,現場需要轉換井平衡性好。
④功率因數控制器
功率因數控制器,主要是采用單片機實時檢測電機電壓與電流之間的相位差變化,控制晶閘管的導通角,自動調節電機的供電電壓,使電機在空載或輕載時降壓運行從而達到提高功率因數,節能的目的。但是在實際應用過程中節電效果不太理想,主要原因是電壓的變化速率跟不上電流的變化速率。另外由于可控硅引起電流產生諧波,受瞬變電勢和瞬變電流的影響,引起電機發熱和振動,影響了節電效果。
⑤無功補償器
無功補償器主要是采用加裝一定容量的電容器對電網進行無功補償,減少無功電流來提高功率因數,降低供電變壓器負荷,從而降低網損達到節電的目的。目前這種技術應用比較廣泛,效果也較好,缺點是不能提高電機效率,也不能降低電機輸入功率,功率因數提高到0.5~0.6,電容器容易損壞。
⑥變頻控制器
變頻控制柜是實現了電動機的軟啟動,對電網無沖擊,電動機功率因數可由0. 25~0. 50 提高到0. 90以上,從而減輕了電網及變壓器的負擔,降低了線損。操作方便,不需停產即可根據油井的實際供液能力,動態調整抽取速度。利用最新研制的四象限矢量控制變頻調速器,配以過程控制、位置傳感等技術改造現有的抽油機,可以實現油井節電、增效和增產,從而提高整個有桿抽油系統的機采效率。
2、優化參數分析
優化抽油參數是根據油井動態變化,以低能耗為目標及時調整抽油參數。做法是長沖程、低沖次、合理泵徑。選擇低沖次的方法是很重要的工作。
常規抽油機生產時油井平均沖次計算公式:
式中: s—電機轉差率;
—電源頻率,hz;
—電動機的磁極對數。
調換小直徑皮帶輪是現場普遍采用的方法,成本低,使用方便,除非換12極電機否則最多能降到4次/分。增加抽油機減速箱傳動比有兩種方法:一種是更換大總傳動比更大的減速箱,傳動比至少要達到32;另外一種是對減速箱技術改造,在原減速箱基礎上更換短齒齒輪。這兩種方法成本高,不宜在現場使用。
換減速箱大皮帶輪直徑成本較高,可操作性差。
表2 降低電機轉速方案對比
綜上所述,對比可實施的幾種方案(表2),從優選節能設備和優化生產參數的角度考慮,對于一些低產井和液面波動大的井,由于受到皮帶輪最小包角和沖次有級調整的限制,達不到供排合理的抽油機井使用變頻控制柜是最理想的選擇。
三、抽油機井變頻調速適應性分析
1、變頻對輸入功率影響
輸入功率 與油井工作制度關系可以用下式表示:
上式表明:影響輸入功率大小關鍵因素是沖程和沖次乘積,也就是光桿運行速度。其它參數不變,油井能耗與抽汲速度成正比。沖次將隨著電源頻率的改變而改變,而且兩者的變化為正比關系。因此調低頻率油井輸入功率降低。
評論